With the European Pharmacopoeia updating its guidelines in 2017, manufacturers now have a choice of methods beyond the traditional distillation systems to produce water for injection (WFI). Here we look at what the options are and what customers need to consider when making their choice.
Water for Injection (WFI) is a very high-quality type of water used for the preparation of pharmaceutical solutions, washing and cleaning of equipment and containers used in the production of medicines, and for the preparation of single doses useful for the dilution of concentrated and lyophilized pharmaceutical substances in order to obtain the desired concentration for medical use. Given its especially delicate purpose, WFI production is subjected to very stringent quality standards.
The production of water for injection
Until 2017, to comply with the main pharmacopoeias, water for injection had to be produced with heat through distillation. After that year, it was introduced the possibility of producing water for injections via membrane filtration systems, and therefore, at cold temperatures.
Distillation is a thermal process that uses boiling and steam condensation to separate non-volatile contaminants. Its key advantages are the effective removal of salts, bacterial endotoxins, and particles, as well as the consolidated knowledge of this process by operators. The disadvantages are the high energy and maintenance costs, the possible formation of thermal degradation by-products, the partial removal of dissolved gasses and volatile compounds, and the risk of microbial contamination during storage.
Membrane filtration is a process that takes place at room temperature and that uses semipermeable membranes to remove contaminants based on their size. Its advantages are low energy consumption, reduced operating costs, effective removal of particles, microorganisms, endotoxins and some organic molecules, and less formation of by-products from degradation. The disadvantages include a greater risk of microbial contamination, the partial removal of salts and small molecules, the potential clogging of the membranes over time, higher initial investment costs and the need for rigorous maintenance and validation.
Hot water for injection: Polaris™ 2.0 MED
The Polaris™ 2.0 product range includes two skid-mounted systems for the production of pure apyrogenic steam or hot water for injections. In this case, we will focus on the Multiple Effect Distiller (MED) for hot WFI production.
Polaris™ 2.0 MED’s operation is based on high-pressure distillation with “falling film” heat exchangers, to speed up the pre-heating phase. Feed water is also used to condense the produced pure steam and to partially cool down the water for injection in order to recover energy within the system.
Polaris™ 2.0 MED was designed in accordance with the European and US Pharmacopoeia and following the EN 285 European legislation about sterilisation, as well as being equipped with a validated software to ensure compliance with FDA (CFR 21 Part 11) and with GAMP V. Furthermore, the system is efficient in terms of operational costs thanks to the "falling film" process and because of the 10% blowdown, and it also offers flexible options to meet each customer’s specific needs.
Finally, Polaris™ 2.0 MED was designed to reduce industrial steam and cooling water consumption, making it more sustainable.
Thanks to its characteristics, Polaris™ 2.0 MED represents a reliable and consolidated solution for the production of hot water for injections, making it an ideal choice for all pharmaceutical and biotechnology companies.

Cold Water for Injection: Orion™
Orion™ is a system designed for the production of purified water and cold water for injection, compliant with the main global pharmacopoeias (European, US and Japanese). This skid-mounted system works with water softening, reverse osmosis and continuous electrodeionisation (CEDI) technologies to support our customers in the pharmaceutical, healthcare and biotechnology sectors. It meets their needs by providing compliant performance in terms of quantity and quality while ensuring microbial control through sanitisation with hot water at a temperature above 80°C. Furthermore, the purified water treatment system Orion™ is designed and manufactured in accordance with International Society for Pharmaceutical Engineering (ISPE) guidelines regarding water and steam and it’s also fully compliant with the FDA, cGMP and GAMP requirements.
Finally, sustainability is Orion's strength. This technology supports you in addressing your environmental challenges, thanks to the use of 99% recyclable materials, CO2 emissions reduction, reduced energy consumption and the recovery of 40% of water.
Thanks to its characteristics, Orion™ represents a cutting-edge solution for the sustainable production of purified water and cold water for injection, making it an ideal choice for all applications that require very high-quality water.

Conclusions
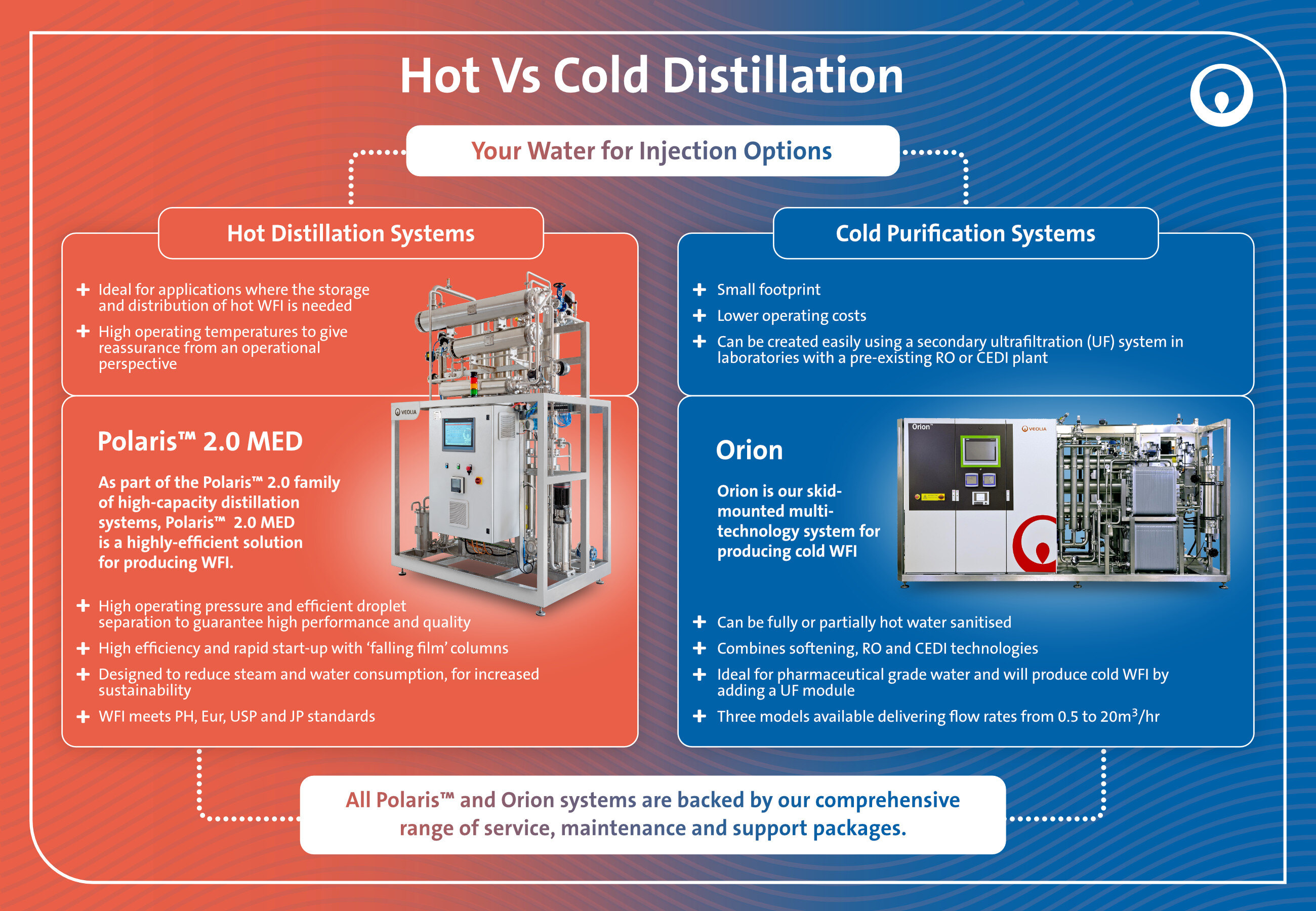
The main difference between cold and hot water for injection lies in the temperature at which the water is produced and distributed.
Usually, cold WFI is especially suitable for applications where you need to avoid potential degradation or alteration of heat-sensitive pharmaceutical compounds. Alternatively, hot WFI is often used for production plant cleaning and for processes that require high temperatures to ensure microbial control. In both cases, it is necessary to meet rigorous quality and purity standards, including microbial content, endotoxin levels, conductivity and impurities requirements.
Deciding between hot or cold water for injection production depends on the specific needs of each production process in the pharmaceutical and biotechnology sector, as well as on the characteristics of the products. Thanks to Orion™ for the production of cold WFI and Polaris™ 2.0 MED for hot WFI, companies can count on systems that comply with the most stringent regulatory standards, while ensuring high levels of efficiency, sustainability and energy saving. Thanks to Veolia's experience and expertise in this field, customers can be assured of the highest quality water for their critical applications, protecting patient safety and promoting eco-friendly production processes.
Contact one of our experts to learn more, here.