When designing cooling tower chemical treatment programmes, the pH levels of the system water have a fundamental role to play in deciding the best course of action. Here, David Broster, Business Development Manager at Veolia Water Technologies UK (VWT UK) answers key questions on the topic and offers guidance on choosing between pH reduction or alkaline treatment programmes.
Why is the pH level of system water so important?.png?width=1200&name=PH%20Blog%20(1).png)
At its most basic, pH is a scale from 1 – 14 that indicates the acidity or alkalinity of a liquid. In the middle of that scale would be pure distilled water, which has a neutral pH of 7. When it comes to process water in cooling towers, operational systems generally operate between pH levels of 7 - 9, depending on the chemical makeup of the water feeding the system.
The pH level of the cooling tower water will have a significant impact on a number of things, two of these being: the tendency for the system water to precipitate scale or induce corrosion, and the performance of treatment chemicals including critical biocides that are used to keep bacterial growth under control.
Companies need to consider the two options – either treat the system as it is, or reduce the pH of the system water in the cooling tower with acidic dosing. Although some sites may be hesitant to manipulate pH levels, this option can bring with it long term value when managed correctly.
Where should customers begin, when deciding to undertake either acid dosing or utilising an alkaline treatment programme?
.png?width=1230&name=Blog%20Headers%20(5).png)
All companies should first start by understanding the chemical makeup of the cooling tower feedwater, by sampling and analysing the water at a certified laboratory. It is also important to understand the full mechanical aspects - such as metallurgy - and operational nature of the cooling system.
Utilising the feed water chemical data we can use a solubility index to help us understand if the cooling tower water is likely to be corrosive or scale inducing to help us decide on a treatment regime. The Langelier saturation index (LSI) allows us to understand this, it is important to note that pH has the single biggest impact on the LSI. Generally, waters with a higher pH tend to be scale inducing and waters at a lower pH tend to be more corrosive.
Biocide efficacy is also impacted by the pH of the water, the two most common oxidising biocides utilised within cooling towers are Sodium Hypochlorite and Sodium Bromide. Both chemicals work well at low pH’s, however as pH increases, the efficacy of Sodium Hypochlorite drops off significantly. At a pH of 8.5 for example, 5% of the Sodium Hypochlorite will be effective, whereas at the same pH, 50% of the Sodium Bromide will be effective. You can start to see just why it is so important to factor in the pH of the cooling tower when designing the treatment regime.
What are the main benefits to highlight?
.png?width=1230&name=Blog%20Headers%20(7).png)
Ultimately there is a huge environmental benefit to running a cooling tower at low pH levels. The main benefits of acid dosing would be reduced chemical, water and energy usage as the cooling tower is at less risk of scale formation and deposition onto heat transfer surfaces. There is also a consequential financial benefit of being able to utilise more cost effective biocides, as well as of course potential reductions in water costs.
When the pH is controlled by dosing acid, we can get more cycles of concentration out of the cooling tower before the water becomes scale inducing. This is because when a cooling tower evaporates heat, it loses water from the system, all the salts within the water become more concentrated as they don’t evaporate, this is what we call ‘cycling up’. As the cycles of concentration increase, so does the pH, this makes the water more likely to precipitate scale. As a result, the cooling tower has to be bled and made up with fresh feedwater to reduce the pH to ensure heat transfer surfaces do not experience scale precipitation. Instead of bleeding the system, pH control on the cooling tower allows acid to be dosed in order to sustain a low pH level whilst the cooling tower cycles up, thus allowing a cooling tower to use less water to cool the same heat load whilst reducing the risk of scale precipitation.
The process of cooling can contribute in excess of 60% of a factory's entire water usage in some industries. If we increase the cycles of concentration, we reduce the make up rate to the system whilst the evaporation rate remains constant on the plant. Furthermore, by reducing the make up rate of water we also reduce the blowdown rate of the system. This means we save water and energy on the make up water (typically £1 per 1000 Litres (M3 ) and also water and energy on the blowdown water (typically £1 per 1000 Litres (M3 ).
The below graph outlines the savings to be unlocked by increasing cycles of concentration within cooling towers across an industrial site. Industry will evaporate millions of tons of water to help produce steel, cars, food, beverages and much more every year, from the below table you can see that increasing cycles of concentration across all cooling towers on site from 2 cycles to 8 cycles would reduce water usage by 43%, whilst maintaining the same rate of evaporation. This of course could be seen as a slightly extreme example, but it isn’t unheard of in the industry. However, even by increasing the cycles of concentration from 2 to 5 cycles, we would reduce water usage by 37.5%. This increase in cycles of concentration can be unlocked by understanding the pH of the system!
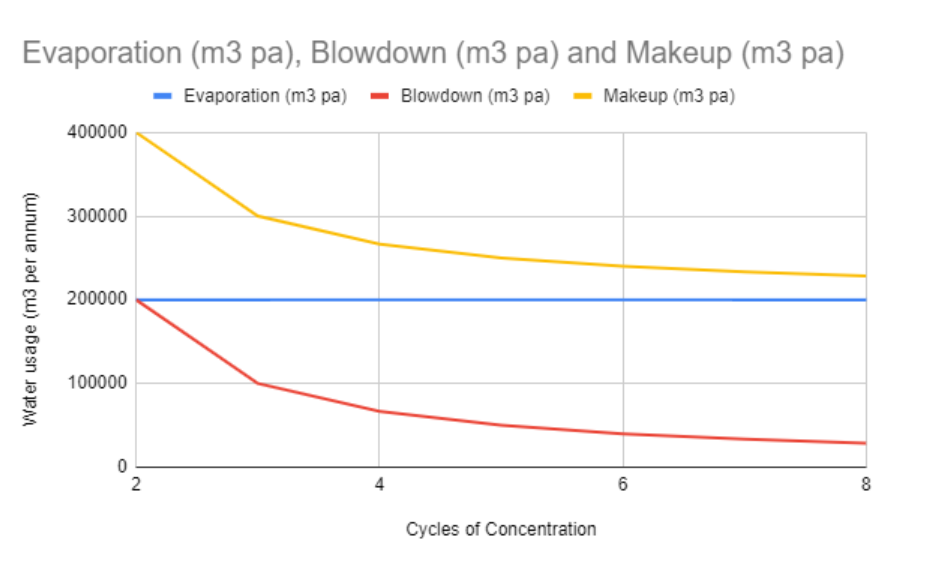
One added bonus to running a cooling tower system at a lower pH is that Sodium Hypochlorite would be efficient enough to use as the primary oxidising biocide alone. This is a much more cost effective biocide programme as currently the cost of Sodium Bromide is anywhere between five or ten times the price of Sodium Hypochlorite. So if we loop back, by reducing the pH we can utilise Sodium Hypochlorite instead of other expensive biocides and we can also run the cooling tower at higher cycles of concentration thus saving money on water, chemicals and energy! Compliant and sustainable. Read more about how you can environmentally run a cooling tower, here.
Finally, does VWT recommend acid dosing or alkalinity treatment?
.png?width=1230&name=Blog%20Headers%20(8).png)
While there are some cases where treating cooling towers with increased pH waters might be the best option, the vast majority of industrial facilities would benefit from a more cost-effective treatment programme through acid dosing. Not only this, but process efficiency can be maintained while using less chemicals and less energy, providing further savings.
It should be noted that well-designed dosing equipment is crucial to prevent system overdosing. As dosing acid is a corrosive hazard, industrial facilities must also ensure compliance and that the acid is stored and delivered safely onsite.
With this in mind and the added complications acidic dosing can bring, it is understandable that companies will be risk adverse and hesitant to make a change. However, with the right provider and support, it can be done, producing significant cost savings while maintaining compliance and staff safety.
VWT UK is an industry leader in water treatment that can perform the analyses required to produce a tailored chemical dosing programme for your cooling towers. A proud member of the Legionella Control Association and an accredited supplier of all the chemical products, control and dosing equipment, VWT UK is in an ideal position to consult and ensure your cooling towers are treated correctly.
For more information on Veolia Water Technologies UK and our wide range of solutions, visit: https://www.veoliawatertechnologies.co.uk