The latest generation of the skid-mounted modular system features core technologies of softening, reverse osmosis (RO) and continuous electrodeionisation (CEDI) with a range of additional treatment options including pre and post-ultraviolet (UV), filtration, degassing and ultrafiltration (UF) for cold water for injection (cold WFI). The three models in the Orion® III range can achieve flow rates from 0.5 to 20 m3/h of purified water or cold WFI that reliably meets the current US Pharmacopoeia (USP) and European Pharmacopoeia (Ph. Eur) standards. It is also fully compliant with FDA, cGMP and GAMP requirements as well as the ISPE guidelines for water and steam.
One of the biggest concerns for users of pharmaceutical-grade water is the risk of biofilms forming within the water purification system, treated water loop or distribution tanks and pipework. These biofilms pose a serious risk and can be very difficult to remove once established. One of the key benefits of the Orion® system is that it has been designed with vigorously tested components for regular hot-water sanitisation at temperatures above 80°C. Therefore, the Orion® systems provide a complete, validated packaged system for sustainable, reliable and consistent production of purified water or cold WFI production.
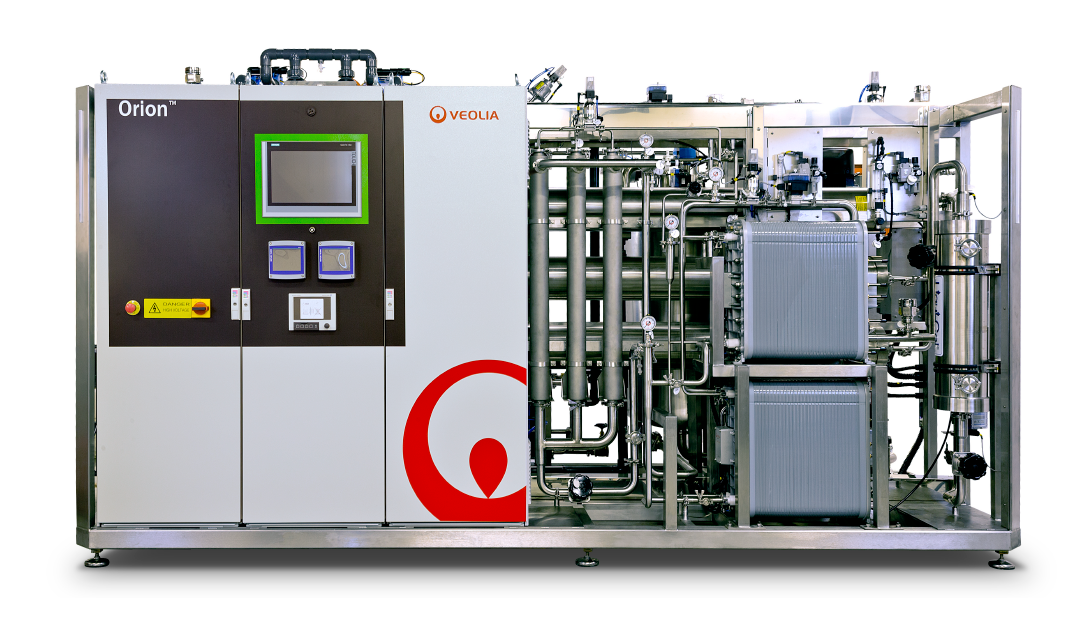
As in almost every sector, pharmaceutical businesses are increasingly looking for solutions that can help them to reduce their environmental impact, including water and energy usage. With the Orion®, up to 40 per cent of wastewater can be recovered and recycled. Similarly, users benefit from reduced levels of energy consumption, with as much as a 50% reduction in total energy usage, as well as a 30% reduction in carbon footprint, in comparison with alternative solutions. The environmental footprint has also been considered with 99% of materials used having recyclable potential.
Our Hubgrade® digital services platform can be used with the Orion® to provide remote monitoring, analysis and optimisation of system performance. Hubgrade® is a flexible tool that connects, monitors and supports our customer activities giving them digital assurances wherever they are. With Hubgrade, we address the water optimisation needs of pharmaceutical facilities, responding to the operators’ and managers’ daily challenges on the whole water cycle (e.g. reduce operating costs while maintaining the required quality of water).
-png-1.png)
Hubgrade® enables remote management with real-time data 24/7, lowering energy, water and chemical consumption, minimising downtime and maintenance, increasing capacity without additional investment, ensure compliance at all times and reducing risk.
The overall performance of your business depends on having a compliant water treatment management system that remains efficient and cost-effective. Veolia Water Technologies has vast expertise to support you with this challenge, including digital monitoring tools that give you real-time facts to guide your decisions.
For two decades, the Orion® systems have reliably delivered fully compliant pharmaceutical-grade purified water to customers for a wide variety of applications. Find out more about the Orion® range by clicking the button below: