Pharmaceutical water compliance continues to challenge manufacturers, with increasingly complex regulations and rising operational costs putting pressure on facilities of all sizes. For decades, companies have grappled with maintaining consistent water purity standards while managing limited resources, space constraints, and the need for specialised personnel. As regulatory requirements become more stringent, many facilities find themselves searching for solutions that can simplify their compliance processes without compromising on water quality or operational efficiency.
What is Pharmaceutical Water Compliance?
Pharmaceutical water compliance refers to meeting strict regulatory standards for water purity in pharmaceutical manufacturing. As global regulations become increasingly complex, facilities must ensure their purified water systems meet pharmacopoeia standards consistently. This critical requirement affects everything from production quality to operational costs, making it a fundamental concern for pharmaceutical manufacturers.
What Compliance Challenges Do Facilities Face?
Many pharmaceutical facilities, especially smaller operations, face significant hurdles in maintaining compliant water systems. Space constraints often limit installation options, while the high costs of compliance monitoring can strain budgets. Additionally, facilities struggle with:
- Resource-intensive validation processes
- Need for specialised personnel
- Consistent bacteria-free water production
- Ongoing maintenance requirements
How Does the Ionpro™ Solve These Problems?
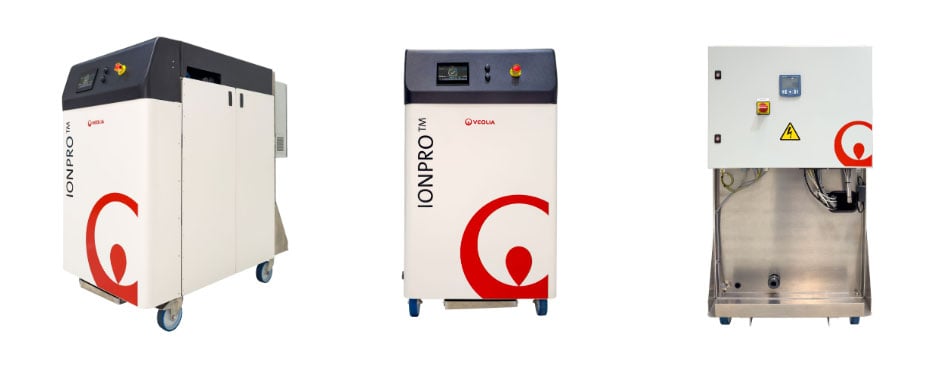
Our latest Ionpro™ system tackles pharmaceutical water treatment through innovative design and technology integration. The system features a compact, single-cabinet design with plug-and-play connectivity, making installation straightforward even in facilities with limited space. Its sophisticated four-stage purification process combines softening, carbon filtration, reverse osmosis (RO), and pharmaceutical-grade electrodeionisation (EDI) to deliver consistently pure water.
Advanced Control Features The next-generation Ionpro™ introduces several significant improvements to system control and monitoring:
- New RO40 controller for precise operation
- Intuitive 7" HMI touchscreen interface
- Emergency stop functionality
- Seamless Hubgrade digital integration
What Makes Ionpro™ Different?
The Ionpro™ stands out through its versatility and efficiency, offering production capacity from 570-1000 l/h with eight customisable options, including CO2 membrane deaeration. This flexibility, combined with digital compliance tracking through Hubgrade, makes it an ideal solution for various applications while reducing the need for specialised operators.
Who Can Benefit from Ionpro™?
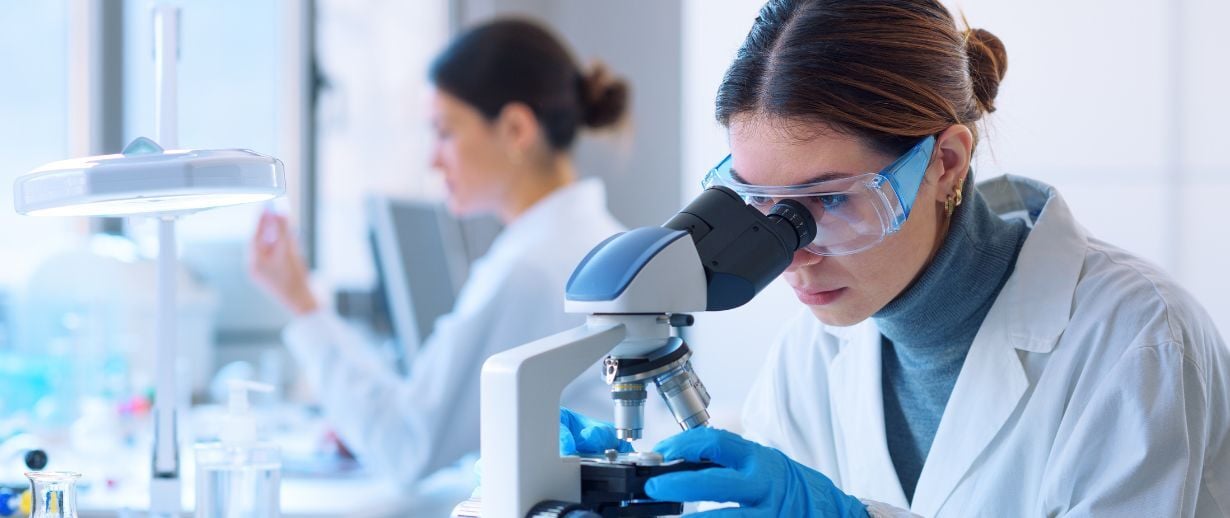
The system's versatile design makes it perfect for multiple industries:
- Pharmaceutical manufacturers
- Research laboratories
- Cosmetics producers
- Microelectronics facilities
- Quality control labs
What is Hubgrade, and How Does it Help?
Hubgrade represents a significant advancement in water system management, combining digital innovation with human expertise. This comprehensive platform provides real-time compliance monitoring and performance optimisation while enabling remote system management. Through transparent quality reporting and expert technical support, Hubgrade ensures facilities maintain optimal operation while meeting regulatory requirements.
Learn more about Hubgrade here: Smart water management starts with Hubgrade
Why Choose Ionpro™?
The next-generation Ionpro™ represents a significant advancement in pharmaceutical water treatment, offering a perfect balance of compliance, efficiency, and ease of use. Its innovative design and digital integration make it an ideal solution for facilities seeking to simplify their water purification processes while maintaining strict regulatory compliance.
Discover how Ionpro™ can transform your facility's water purification process. Contact one of our experts today to discuss how it can benefit you.