Water in cooling water systems must be treated to avoid scaling, corrosion, fouling and microbial growth which can significantly impact overall plant efficiency. In this blog, we turn our attention to our relevant product solutions.
An untreated cooling water system can develop deposits, scaling, corrosion, fouling and microbial growth internally; all of which can negatively impact plant efficiency and worker safety. At Veolia Water Technologies UK, we have developed Hydrex™, an extensive range of water treatment chemicals that can help to control these issues, mitigate the risks and keep a cooling water system running safely at optimal efficiency.
What is Hydrex™?
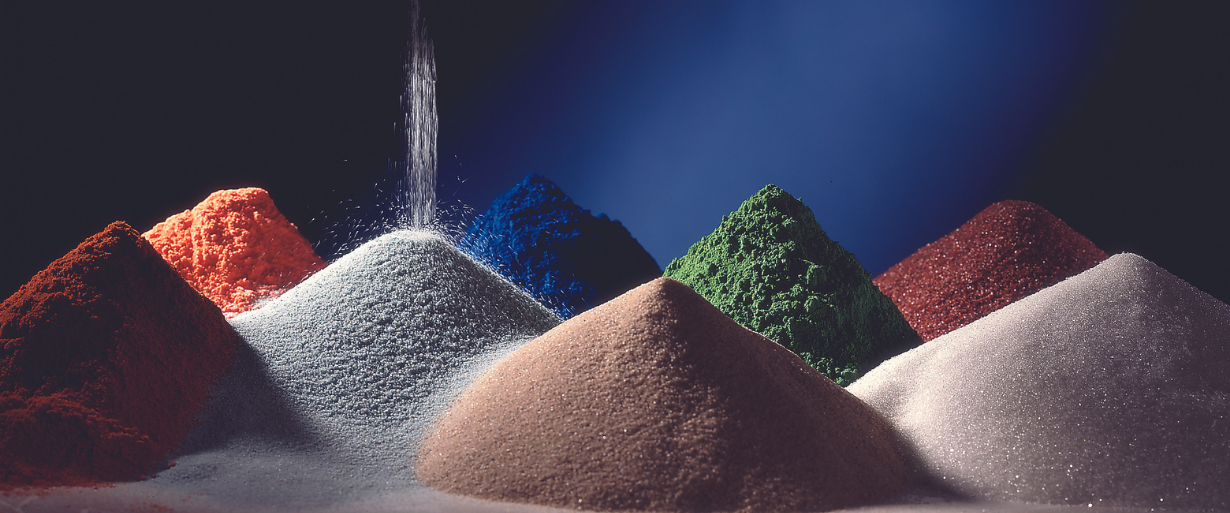
The comprehensive Hydrex™ range includes both organic and inorganic chemicals and features more than 3,000 formulations. Each of these formulations has been designed to meet a variety of individual needs within the industrial and institutional sectors.
The Hydrex™ 2000 series has been specifically designed to provide an effective solution to the most common cooling water issues. It comprises of scale inhibitors (phosphorus and non-phosphorus based products, homopolymeric dispersants and high-performance polymers), corrosion inhibitors (anodic, cathodic, organic), biodispersants and cooling water cleaning agents. Here is an overview of the most common problems faced and how Hydrex™ chemicals can help:
Deposit Control
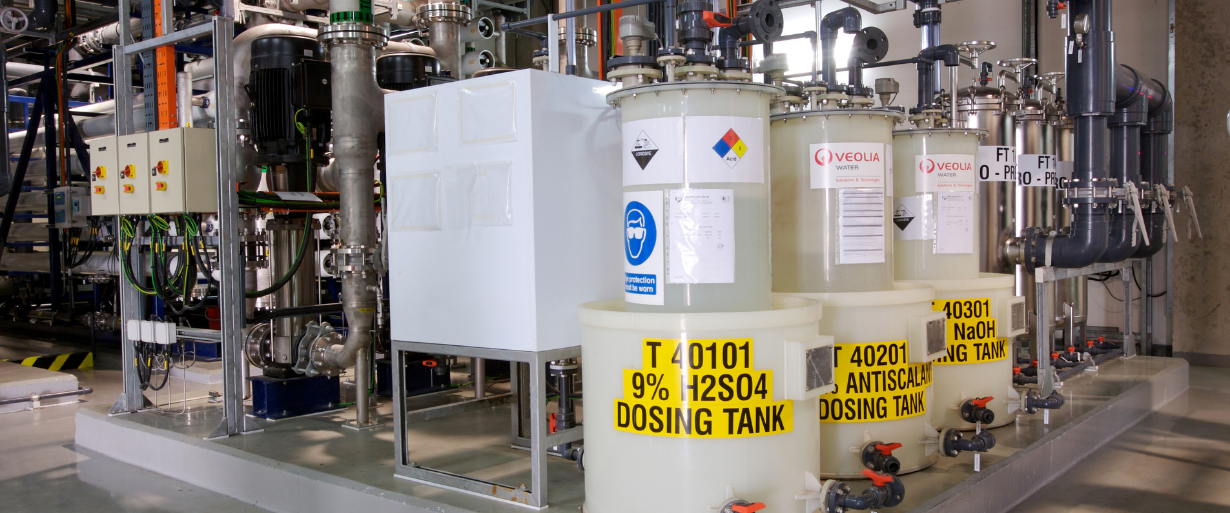
Hydrex™ products are able to keep metal heat exchange surfaces clean, ensuring efficient heat rejection by the cooling system. Hydrex™ cooling water chemical treatments also protect against under-deposit corrosion that can occur in high heat or low flow areas of the cooling system and impact heat exchange and equipment efficiency.
By applying Hydrex™ within a balanced cooling water deposit program, plant operators will see a range of benefits, including increased cooling water flow and optimised heat transfer rates in heat exchange processes. Water consumption will also be reduced, which in turn will lower costs. Furthermore, assets will be protected.
Corrosion Control
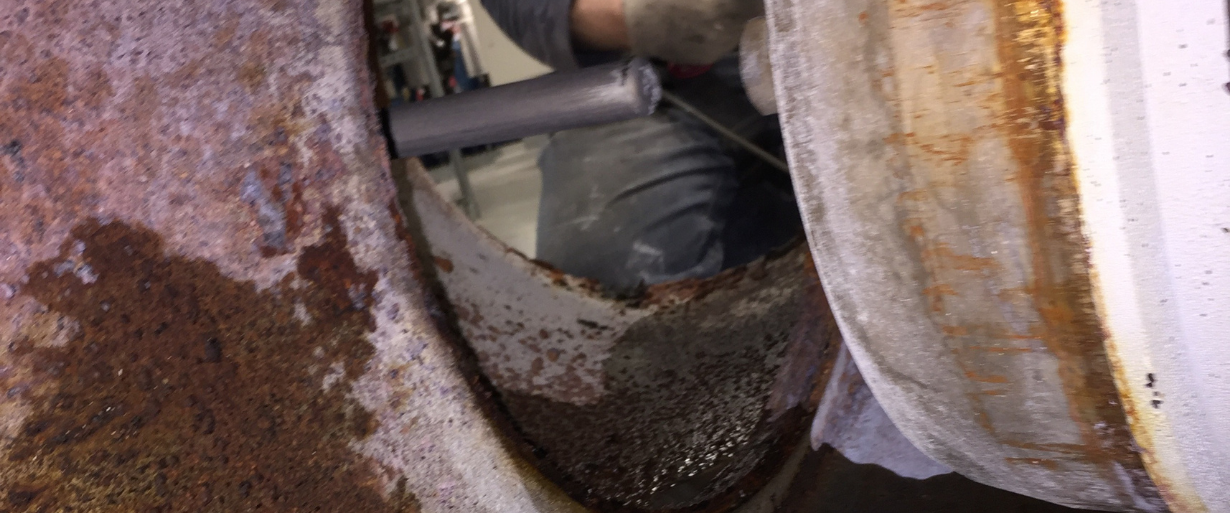
Although there are many different types of corrosion, the majority of cooling system corrosion builds up as a result of one of three types.
Uniform corrosion is a common form of corrosion experienced in industry. It results when oxygen attacks the water/metal interface, leading to a gradual decomposition of the metal. Unprotected, this oxidation will progress and appear as a metal oxide or general rusting of system surfaces. Uniform corrosion can be reduced by the proper application of corrosion inhibitors, coatings, or cathodic protection. Thus, this is the least dangerous and most easily prevented form of corrosion out of the three types.
However, the most common form of corrosion in cooling systems is pitting. This is more aggressive and penetrates the metal within a short period of time when initiated and will result in catastrophic damages to the plant equipment such as heat exchangers.
Galvanic corrosion can be relatively common in cooling systems, this is a specialised form of corrosion that results when two dissimilar metals that are significantly different in nobility are connected and exposed to a common water environment: one metal becomes cathodic and the other anodic, setting up a galvanic cell.
Metal loss will occur at the anode and accelerate through the metal piping or heat exchange surfaces resulting in a visible pitting of the surface. This can be accelerated by different metals coming into contact with each other.
By implementing Hydrex™ chemicals, corrosion is minimised and heat exchange efficiency is maintained. The right Hydrex™ chemical can also help to prevent any production downtime associated with equipment failure due to corrosion and corrosion by-products.
Fouling Control
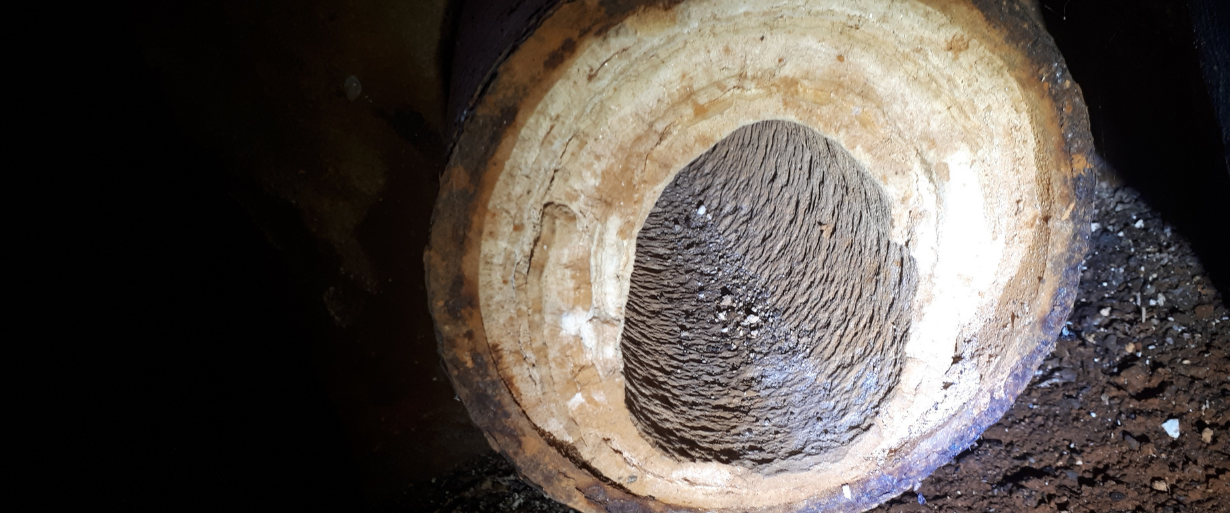
This can be controlled by regular inspections and maintenance on the cooling water distribution deck, the cooling towerfill and cooling tower sump, to ensure that there is minimal build-up of suspended solids.
If fouling continues, VWT UK can deliver a treatment program consisting of Hydrex™ cooling water antifoulants along with an appropriate side stream filtration device on the cooling water bypass line to help remove the micro-foulants. There are many different anti-foulant Hydrex™ formulations that consist of oxidising and non-oxidising biocides, fungicides, algaecides and bio dispersants.
Overall, our comprehensive range of Hydrex™ chemical water treatment products provide options to mitigate issues and improve the performance of a wide variety of cooling system conditions. However, selecting the right formulation and dosage level will require the advice of our specialist team.
If you are interested in finding out about the best option for your site, please learn more here