For the production of highly purified Water for Injection (WFI), manufacturers now have a choice of approaches. Kalpesh Shah, our Head of Sales - Process Water, outlines five key benefits of cold WFI systems.
Since 2017, the European Pharmacopoeia (Ph. Eur) standards for Water for Injection has allowed both distillation (hot WFI) and reverse osmosis (RO) based membrane processes (cold WFI). While distillation has remained the go-to option for many, cold WFI systems, such as our Orion® solution, can provide a reliable and cost effective way of producing WFI using a combination of tried and trusted technologies. Therefore, if your WFI system is reaching the end of its operating life or you are equipping a new facility, it is worthwhile considering all the options.
Utilising proven technologies
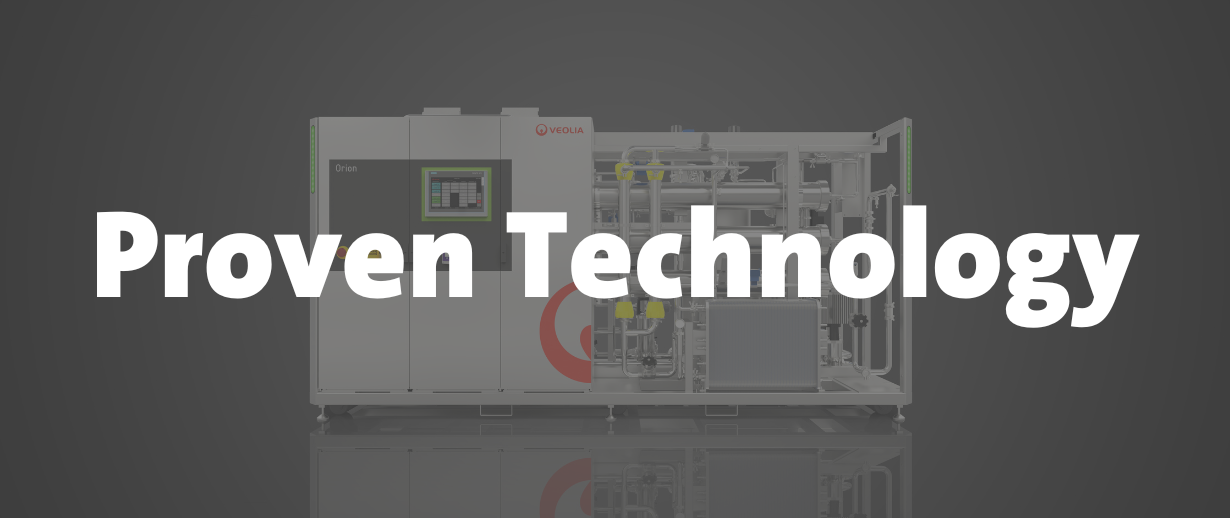
To produce fully compliant WFI, systems such as our Orion® use reverse osmosis (RO), continuous electro-deionisation (CEDI) and ultrafiltration (UF) processes. The RO and CEDI technologies have been used widely in the pharmaceutical industry for decades to produce purified water. For example, Orion®, which was developed specifically for pharmaceutical applications, was first launched over 20 years ago. While it has evolved into the current Orion® III range, the water purification technology it utilises remains unchanged. To produce WFI, the RO and CEDI are used with the addition of a final UF stage. This simple treatment stage consists of hollow fibre membrane with a 6000 Dalton molecular cut off to remove particles as small as protein macromolecules and endotoxins.
Simple compliance
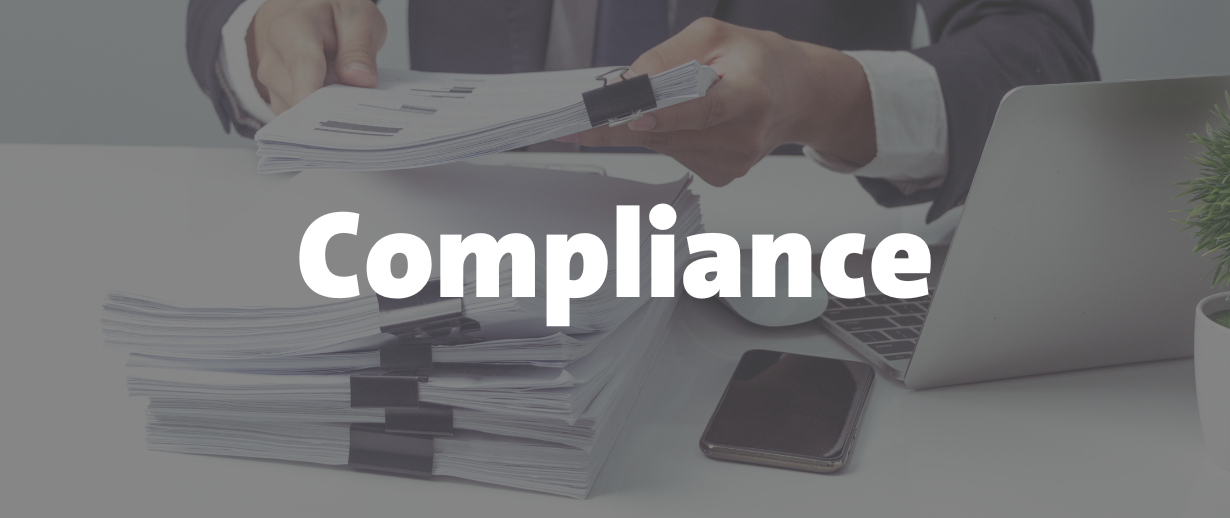
This combination of RO, CEDI and UF technologies is the approach recommended in the Ph. Eur Monograph for cold WFI. While the addition of cold WFI methods was a significant update to the regulations, it simply brought Europe in line with other major regional pharmacopoeias that had long included non-distillation methods, such as the United States Pharmacopeia (USP) and Japanese Pharmacopoeia (JP).
Among the most common concerns with regards to cold WFI is the risk of contamination, including biofilms forming within the RO of the water purification system, which can be very difficult to remove once established. However, this risk can be easily managed with regular hot water sanitisation. With Orion®, the whole system, including the pre-treatment stage and distribution pipework, can be hot water sanitised at temperatures above 80°C. This prevents the growth of these microbes and eliminates the need for chemical decontamination.
Furthermore, careful monitoring, which is necessary with any WFI system, can be made simpler by selecting a solution that supports remote monitoring capabilities. For example, our Hubgrade digital services platform allows easy monitoring from any connected device as well as enabling analysis and optimisation of system performance.
In addition, partnering with a water treatment specialist that can offer full support will help deliver peace of mind. At Veolia Water Technologies UK (VWT UK), our validation package ensures simple compliance with manufacturing criteria such as cGAMP and ISPE guidelines as well as the requirements of inspection bodies, including the FDA and MCA. To provide smooth progression from design qualification (DQ) through to successful completion of the performance qualification (PQ), the documents closely follow the protocols and guidelines laid out by the regulatory authorities.
Lower operational expenditure
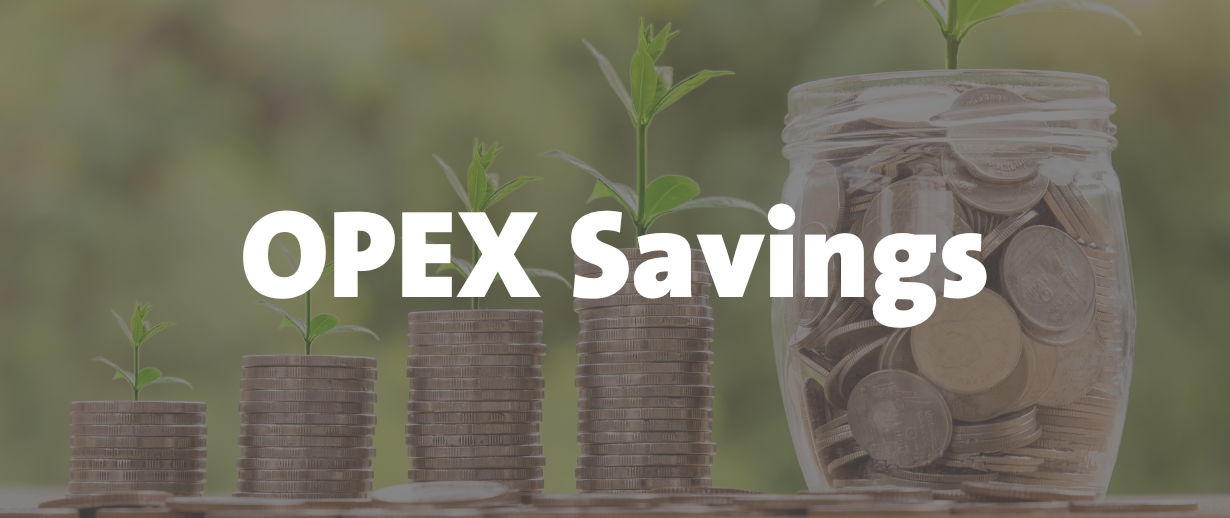
When compared to distillation, membrane based cold WFI systems can provide significant operational expenditure (OPEX) savings. For distillation, it is necessary to heat the water to boiling point to create steam. To change the phase of water in this way requires a large amount of energy, which despite significant improvements in energy efficiency still makes up a large proportion of the cost of producing WFI using this method. In contrast, cold WFI systems operate at ambient room temperature so there is no heating required.
If the water needs to be stored and circulated hot (usually above 80°C) this can still be achieved with a cold WFI system as the water can be heated up to the required temperature. While this will use additional energy, it will be far less than what would be needed to heat the water to boiling point.
Reduced capital investment
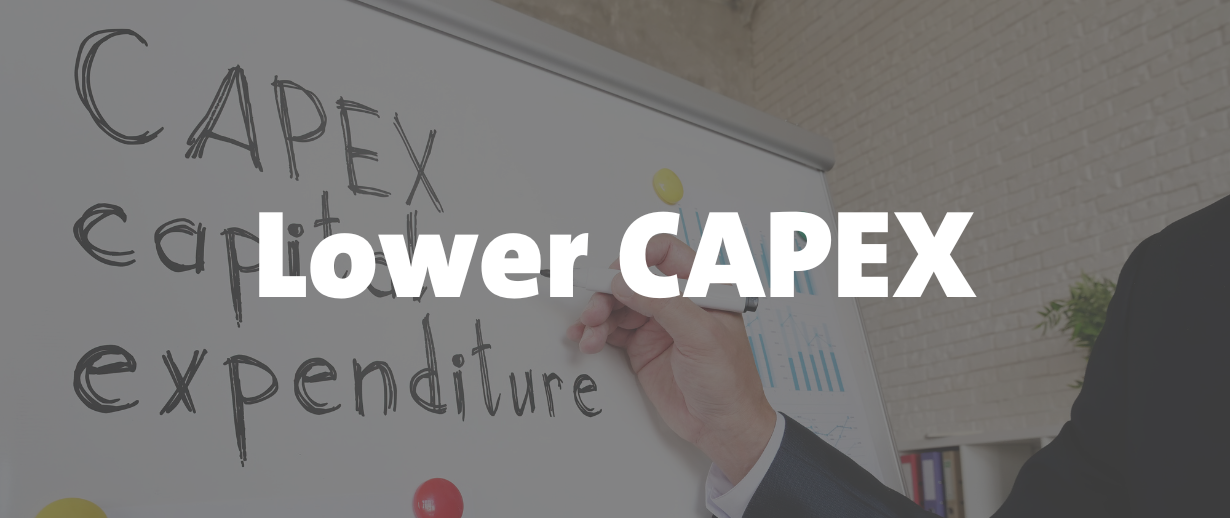
Generally, membrane systems have lower capital expenditure (CAPEX) requirements. This is due to the higher typical cost of distillation equipment plus the required pretreatment. In addition, where there is an existing RO and CEDI system in operation to produce purified water, it may only require an additional secondary membrane filtration stage adding to produce WFI.
Smaller plant footprint
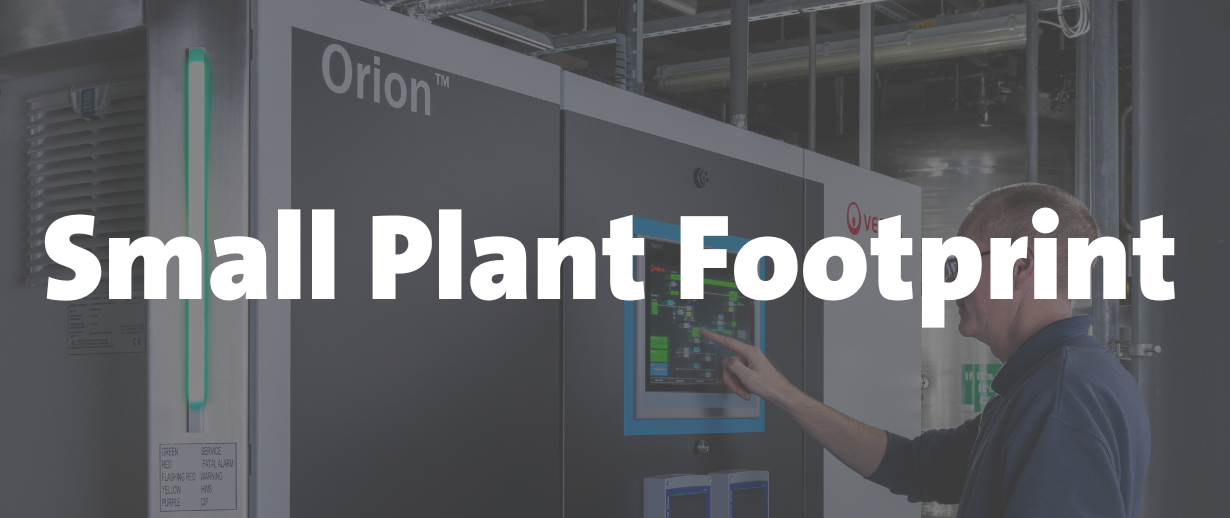
Membrane systems can also offer a space saving solution, which is especially valuable where production is being expanded in an existing facility. Depending on the system, distillation equipment often has a large footprint as it requires additional pretreatment and may require additional vertical space, particularly in the case of Multi Effect Distillers (MED). The nature of cold WFI technology means that these systems do not require the same amount of space, especially if a compact solution, such as Orion®, is chosen.
A reliable solution is essential when producing water for injection. Cold WFI is increasingly being adopted by pharmaceutical businesses to meet CAPEX and OPEX targets using dependable technologies, familiar to those in the sector.
Click here to find out more about our work with other types of pharmaceutical water.