Whisky production is a water-intensive process, requiring about 50 litres of water to produce just one litre of spirit. In 2014, the Scottish Whisky Association reported that the industry used a total of 48.8 million cubic metres of water. Most of this, 73%, was used for cooling and returned to the environment unchanged, except for its temperature. The remaining 13 million cubic metres were used in the production process, with 63% dedicated to process water and the rest for cleaning and manufacturing activities.
Reduce costs by reusing and recycling wastewater
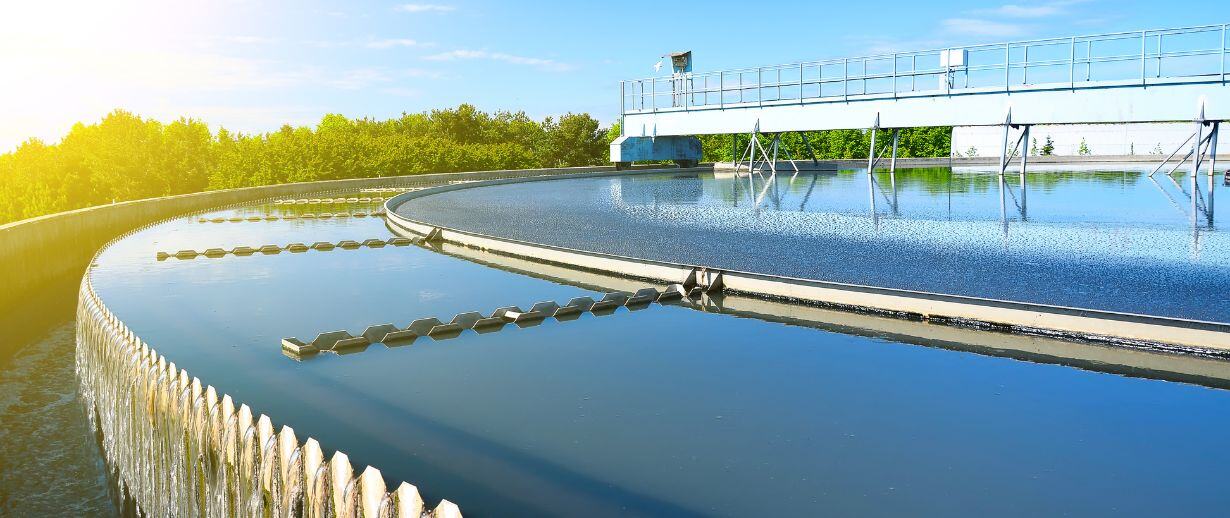
Given that it costs twice as much to discharge water as it does to bring it on site, there is a strong financial incentive to think more creatively about how to use wastewater, particularly as these costs are likely to rise faster than inflation, and there is a growing need to reduce the pressure on local water supplies during seasons of irregular rainfall or drought.
The first step is to realise that wastewater, despite its name, is not useless. In fact, reusing and recycling wastewater is one of the most effective ways of reducing overall water costs. There are plenty of on-site demands, such as boiler feed, cooling towers and some cleaning activities, that can make good use of recycled wastewater after it has been treated.
As of 2024, the use of recycled wastewater as a water ingredient in the beverage industry, particularly in liquor production, remains very limited. While purification technologies such as reverse osmosis and continuous electrodeionisation are capable of achieving high purity levels, the cautious approach persists due to licensing agreements and public perception concerns. The industry continues to navigate these challenges, balancing technological capabilities with regulatory and consumer acceptance.
Resource recovery through anaerobic treatment
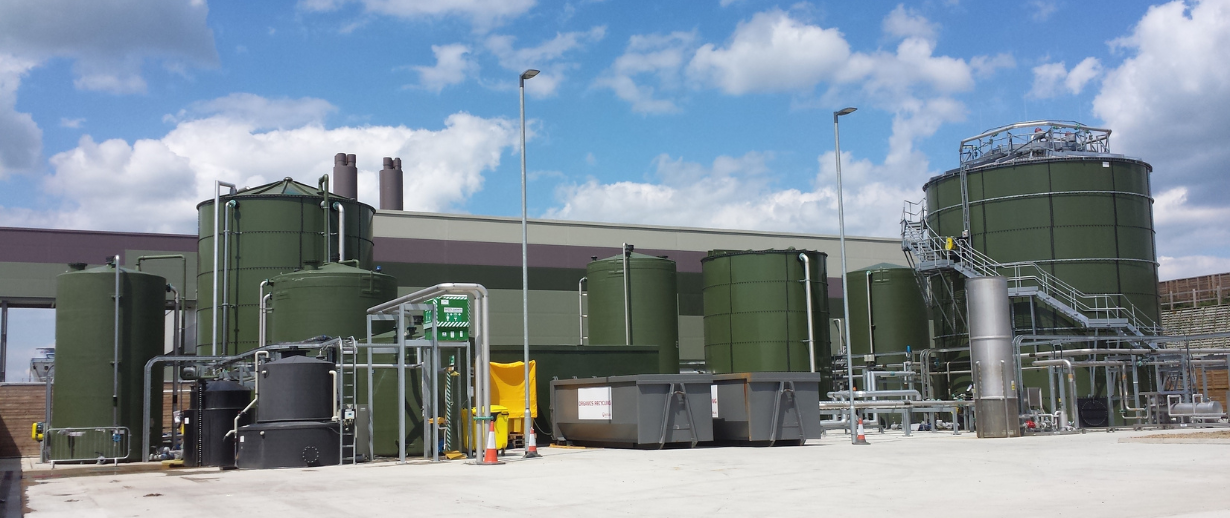
Breweries and distilleries can also benefit from anaerobic treatment of their high-strength wastewater with moving bed biofilm reactors. Biogas is a by-product of this process and can be sent to an on-site combined heat and power (CHP) plant to provide energy (and heat) to run the facility, reducing reliance on non-renewable resources, while offering cost savings at the same time. In some cases, distilleries and breweries are able to produce an excess of biogas and electricity, which can be sold back to the grid. In addition, a second by-product, biomass, can be sold to local farmers as a nutrient-rich soil additive.
There is an extensive range of wastewater treatments available to distilleries and breweries, and every unique situation will require a tailored solution to meet the specific demands for recycling wastewater, taking into account the desired water quality, capacity requirements, the available space and budget.
Partner with Veolia Water Technologies UK to transform your beverage production process with innovative water reuse solutions. Our cutting-edge technologies and expert guidance can help you achieve sustainability goals, reduce costs, and enhance your brand's reputation. Contact us today to learn how we can support your journey towards a greener future.