Distillery operations require careful management of water systems to prevent Legionella contamination. Whether during normal operations, maintenance periods, or temporary shutdowns, maintaining proper water safety protocols is crucial for regulatory compliance and public health.
Understanding the Risks of Legionella in a Distillery
Legionella bacteria in distillery environments pose specific challenges due to the nature of the production process. The combination of warm water systems, particularly in cooling systems and condensers essential to the distillation process, creates ideal conditions for bacterial growth. These systems typically operate in the 'danger zone' temperature range of 20-45°C, where Legionella thrives.
The primary risk comes from the creation of water droplets or aerosols from cooling systems, which can spread contaminated water particles into the air. In a distillery setting, these aerosols can affect not only workers in the immediate vicinity but also nearby communities if the bacteria are present. The risk is particularly significant because cooling towers are often located at height, allowing aerosols to disperse over wider areas.
Evaporative cooling systems, essential to distillery operations, can also create the perfect conditions for Legionella bacteria to thrive if not properly managed. These systems demand rigorous attention through effective cooling tower water treatment processes to control bacterial growth. The presence of organic matter, scale, and biofilm in these systems, all common in distillery operations, can provide nutrients and protection for Legionella bacteria, making control measures even more critical.
Legal Framework and Responsibilities
Anyone who has a part in managing the facilities (dutyholder) has a responsibility to protect employees, visitors and the public from these risks. Employers have a legal responsibility to protect their employees under the Health and Safety at Work Act 1974 and the Management of Health and Safety at Work Regulations 1999. Furthermore, the Control of Substances Hazardous to Health (COSHH) regulations include biological hazards such as Legionella. Health and safety law also makes businesses responsible for protecting the public from any hazards that arise due to their operations.
What should be done?
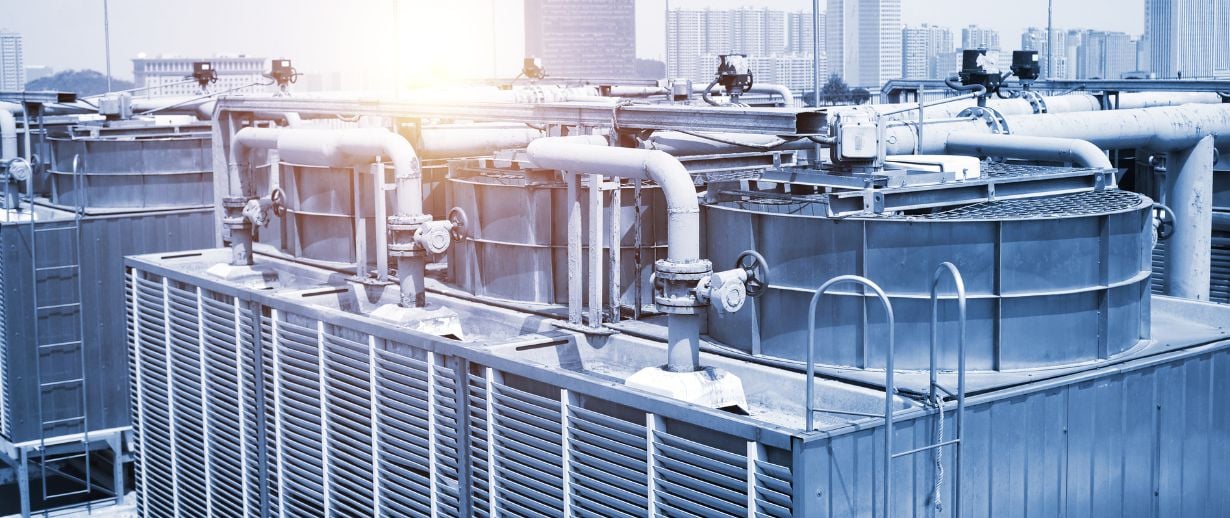
When cooling systems need to be temporarily suspended, proper shutdown procedures are essential. The Health and Safety Executive’s (HSE) guidelines on Legionella control in these systems (HSG274) provides specific advice for the temporary shut-down of equipment. It recommends that if the system is to be kept out of use for under a month, biocide water treatment chemicals should be circulated through the system regularly, at a minimum once a week. If the suspension of activity is going to be longer than one month, then it should be drained and shut down in line with the site’s Legionella control scheme.
It is essential that where systems remain operational, the normal safety procedures are still followed. This includes:
- Regular monitoring and testing
- Consistent water treatment
- Scheduled equipment cleaning
- Comprehensive record-keeping
If this cannot be completed due to staff shortages or other restrictions, then the production process has to be halted and the cooling system shut down. To continue without the correct measures in place risks the health of employees and the public.
Recommissioning with Confidence
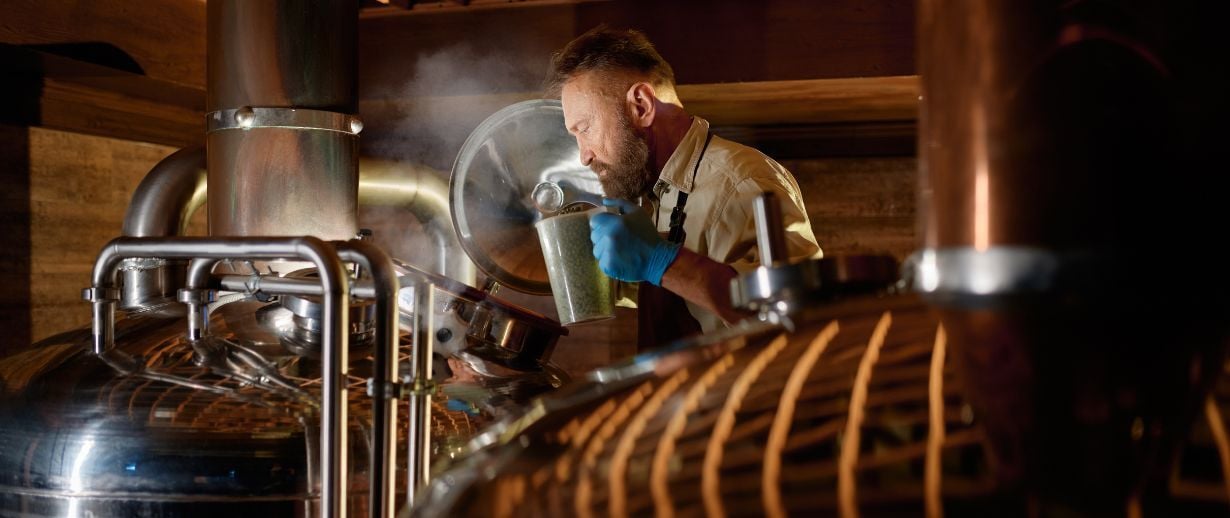
When a plant that has been shut down is required again, it must be recommissioned correctly in line with the HSE guidance HSG274. It states that recommissioning should only be carried out when the system will be immediately brought back into use, and it should not be refilled with water until recommissioning begins. The guidelines also require records to be kept of the process and for independent verification of the test results, such as by an engineer.
In addition, distilleries should look at their servicing schedules to make sure that regular checks and maintenance are still being carried out where necessary. This will help ensure an issue-free restart of the systems when operations resume.
How Veolia Water Technologies can help
We have vast specialist expertise and experience in industrial water treatment chemicals, and in particular, control of Legionella. We are an accredited member of the Legionella Control Association, and our extensive experience working with distilleries in all areas of water treatment means we understand the importance of getting this right.
Maintaining effective Legionella control in distillery operations requires constant vigilance and adherence to established protocols. By following these comprehensive guidelines, facilities can ensure both regulatory compliance and the safety of their operations, employees, and the public. Regular review and updates of these procedures, combined with professional support when needed, create a robust framework for managing water safety in distillery environments.
To find out more about the products, support and services we can offer, see here.